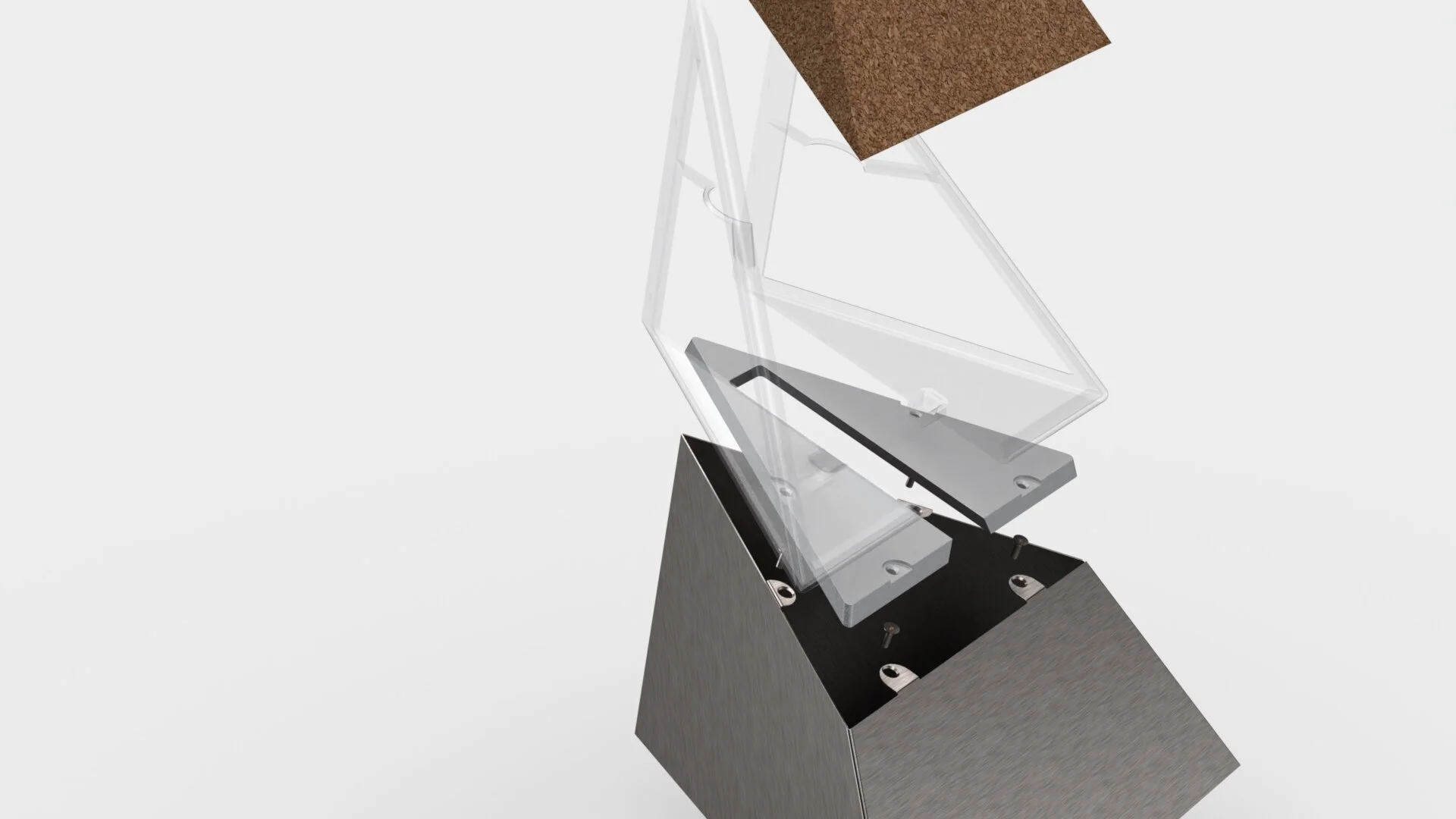
Topz Industrialized: Redesign from a Manufacturing Stand Point.
From Material selection to process definition - We considered what it would take for full-scale Production.

The lamp was redesigned as a group. This project was aimed at making it possible to produce the product at scale. This included materials and process research, manufacturing design in each component, technical documentation, applicable standards and patents, factory layout and financial analysis.

The part shown was my main focus, considering constant wall thickness, draft angles for the chosen LM24 alloy. The images also show even pressure distribution, weld lines and potential overflow well locations in the final design, using Solidworks simulation using casting and material values.

The redesigned light bulb holder would be injection moulded from two snap fastened, colycarbonate components. The textured top and bottom panel could be sustainably made from a cork polymer compound, also by injection moulding, whilst the 1mm stainless steel base is manufactured by a series of punching, notching and bending steps, before being welded.
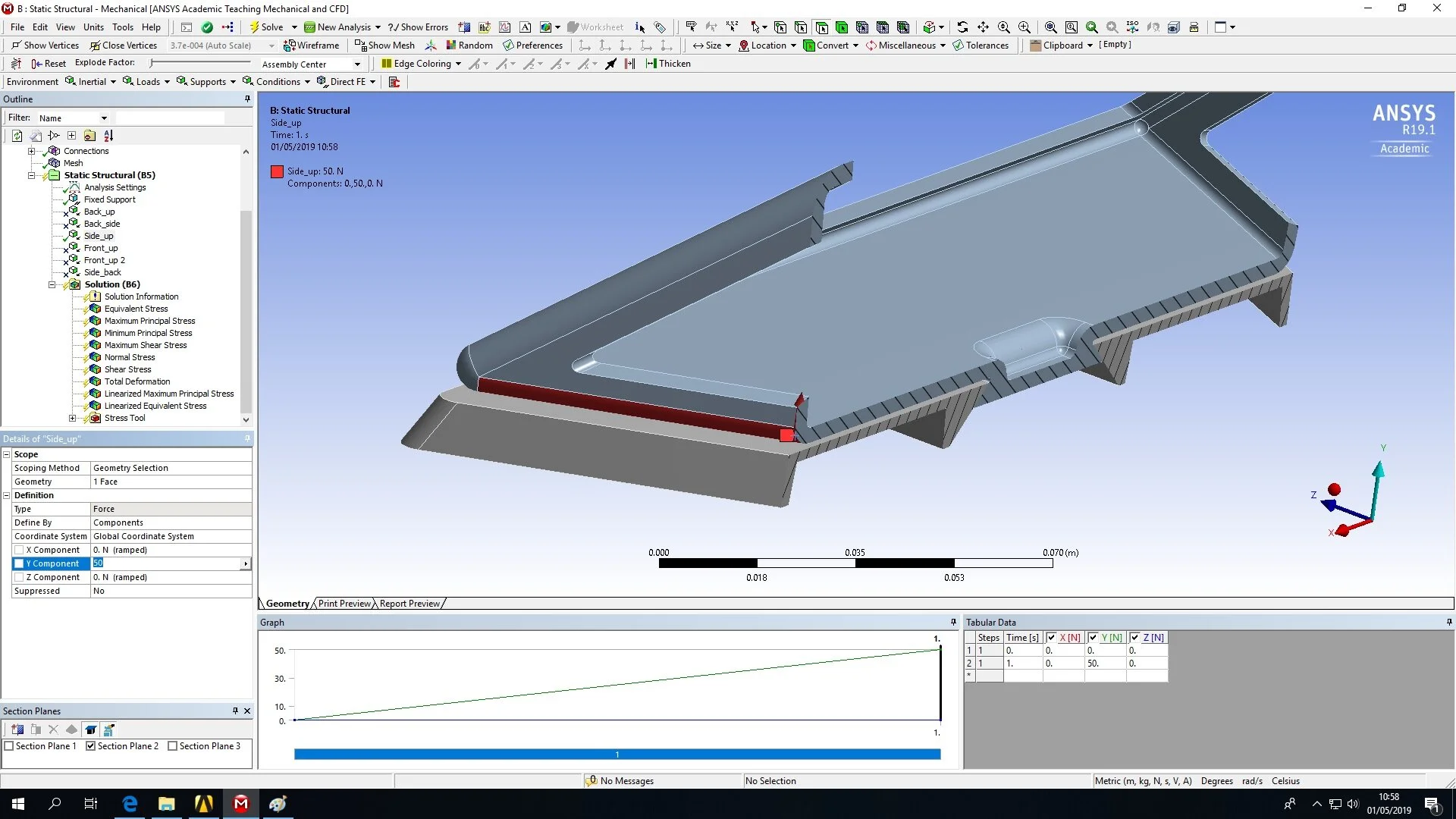
Further to this project I conducted static stress analysis in Ansys to assess the strength of the dovetail element connecting the upper and lower sections. Loads were applied in various locations to assess damage. This concluded that the dovetail needed to be 30% wider and a supporting strut was incorporated.
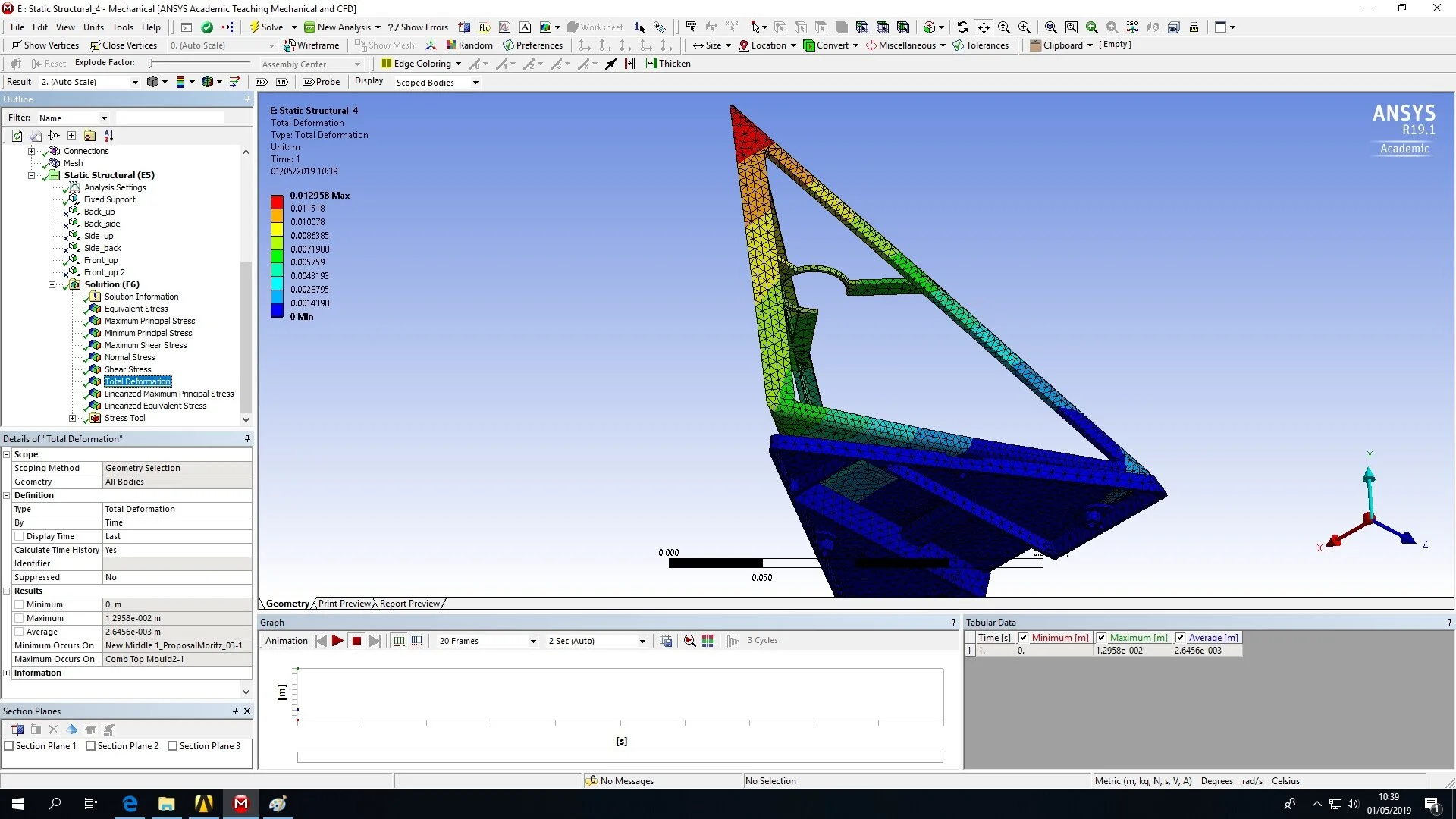
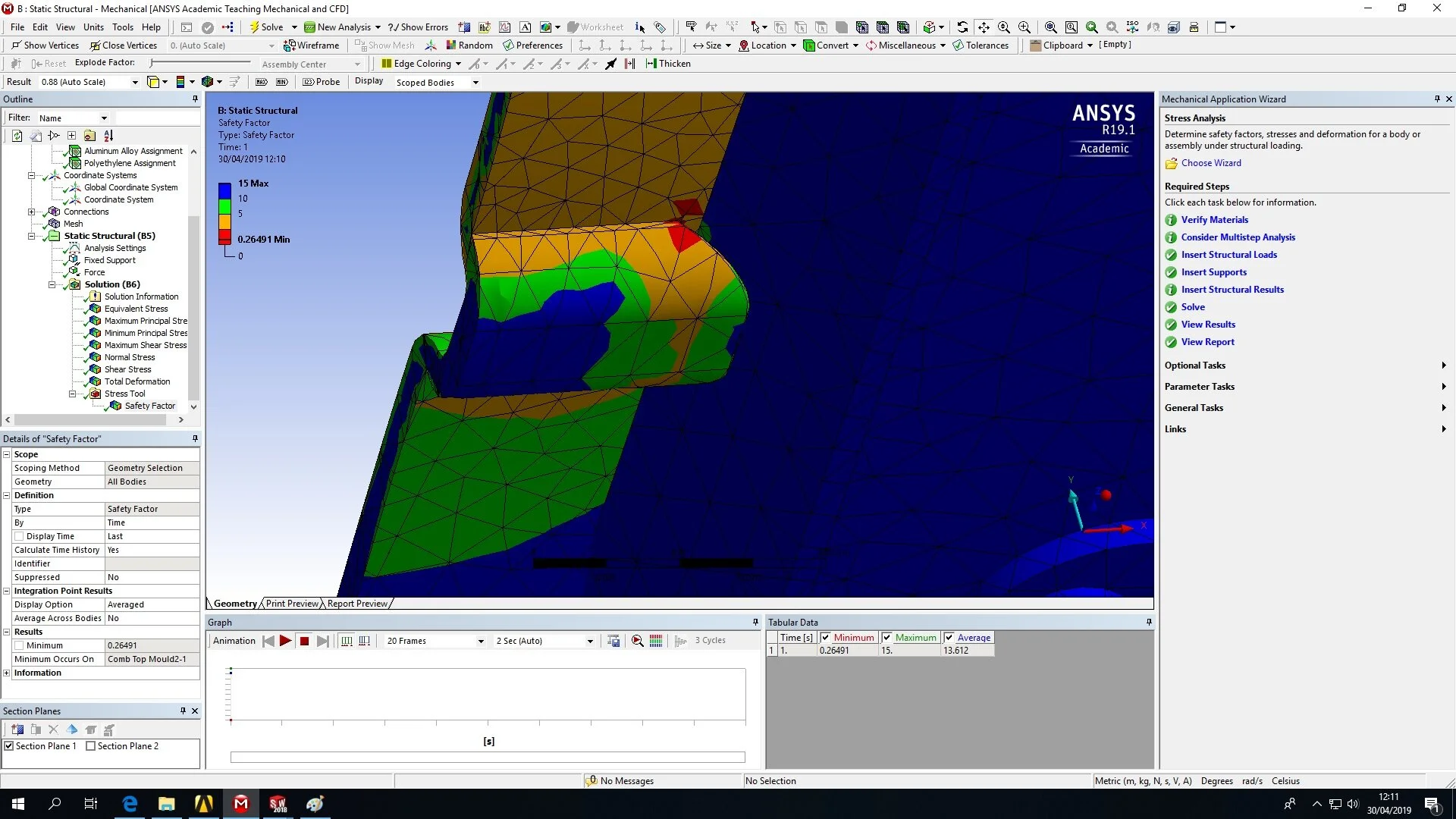

Resulting from this the factor of safety for the most destructive load (at the front edge) was increased from less than 1 to 2 at 20N of force. This should make accidental damage to the part less likely during use.