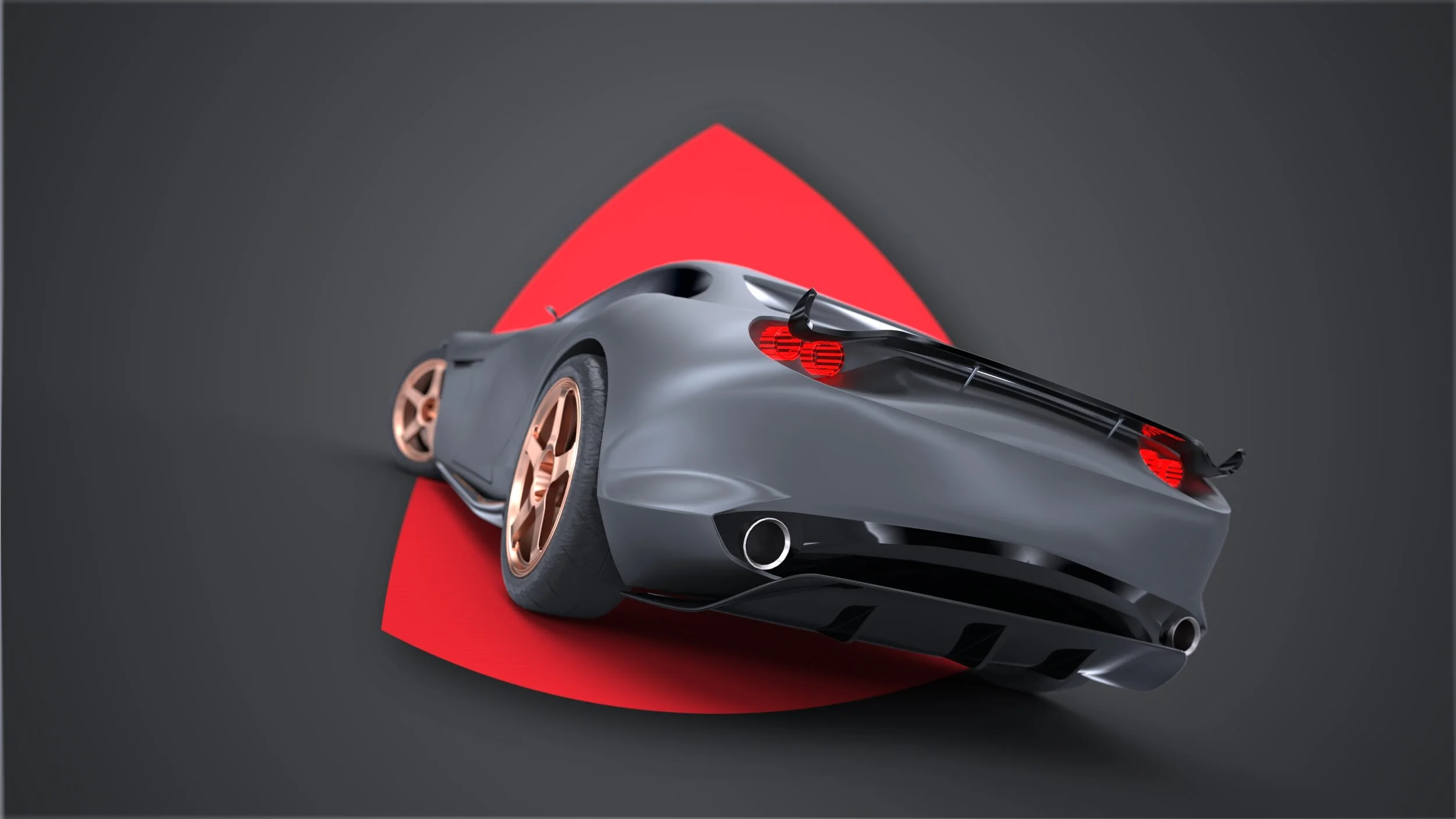
Mazda RX-Vision:
1:40 Model
A process for continuous curvature boundary representation and rapid prototyping
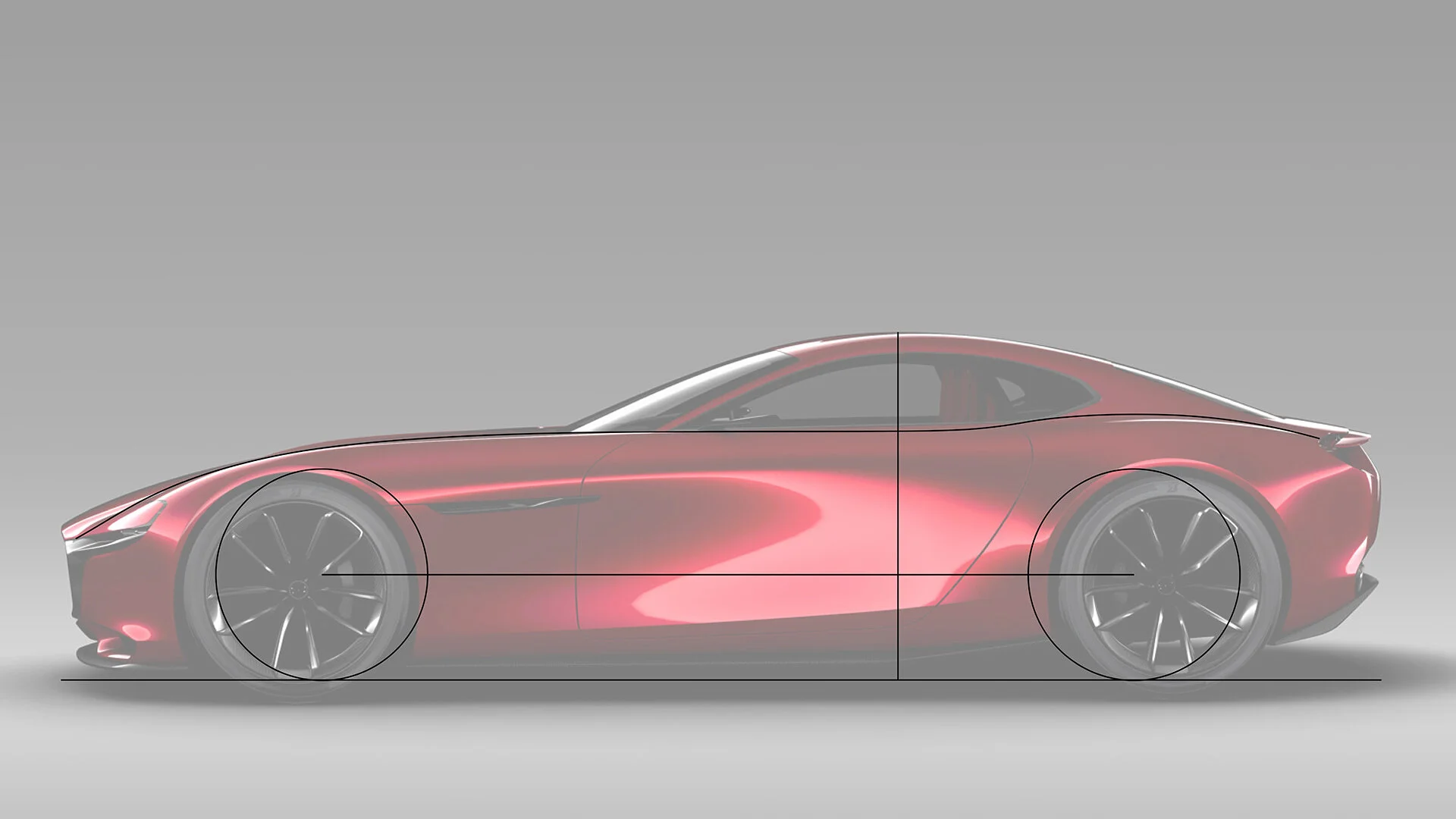
Blueprints are created to according to the dimensions of the original vehicle and visual modifications are made.
Using straight lines, a mesh is created over the blueprints and original images are overlaid.
Next, the splines describing the body curvature are overlaid which can be later adjusted using the underlying geometry.

This is similarly done across the width of the car by placing planes on the edge points of the base mesh.
Surfaces are created within the boundaries of the splines and curvature is validated. Once patched into a solid volume fillets are added on any edges.

Additional parts are modelled with configurable thicknesses to stay within minimum process capabilities.

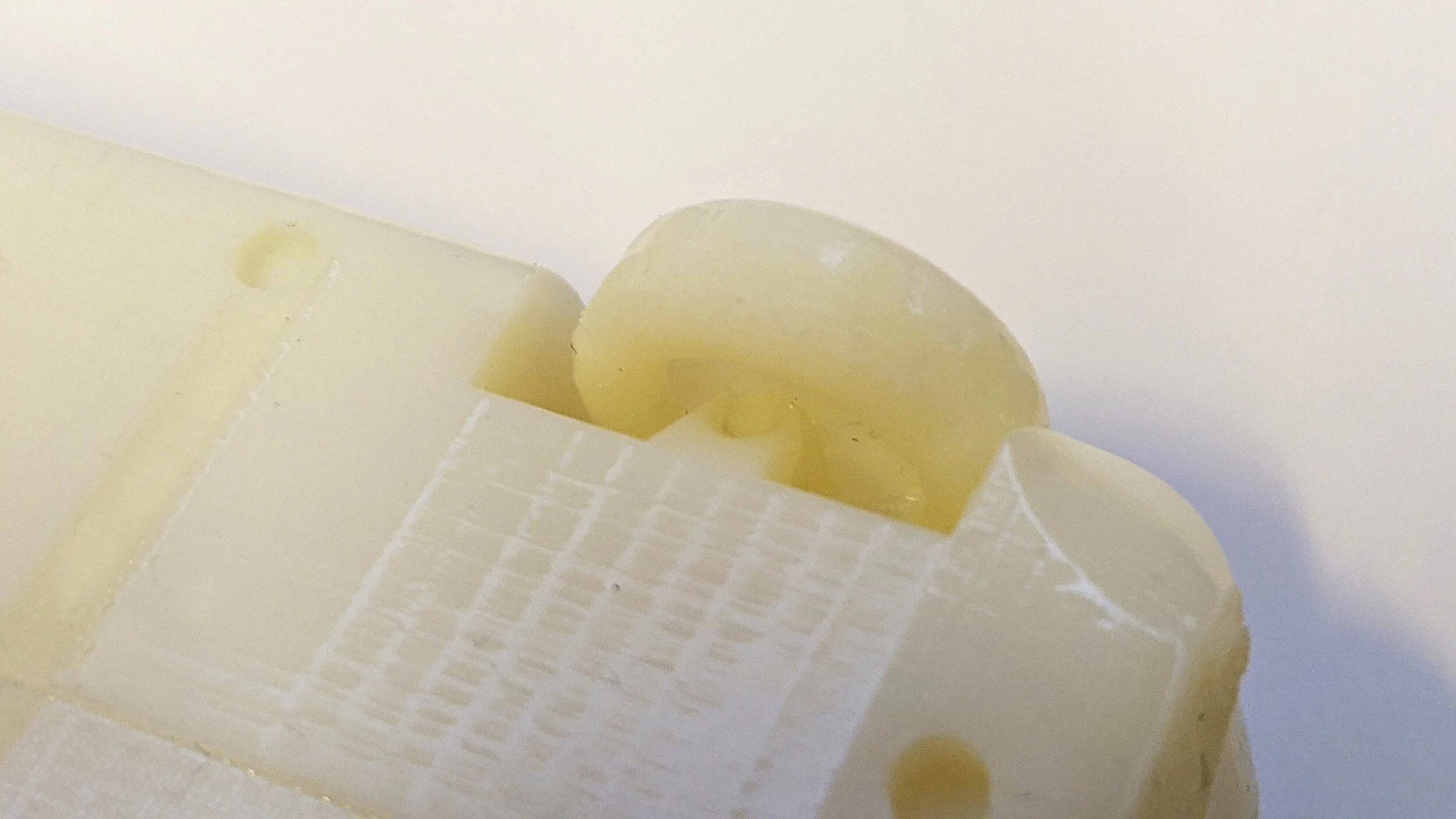

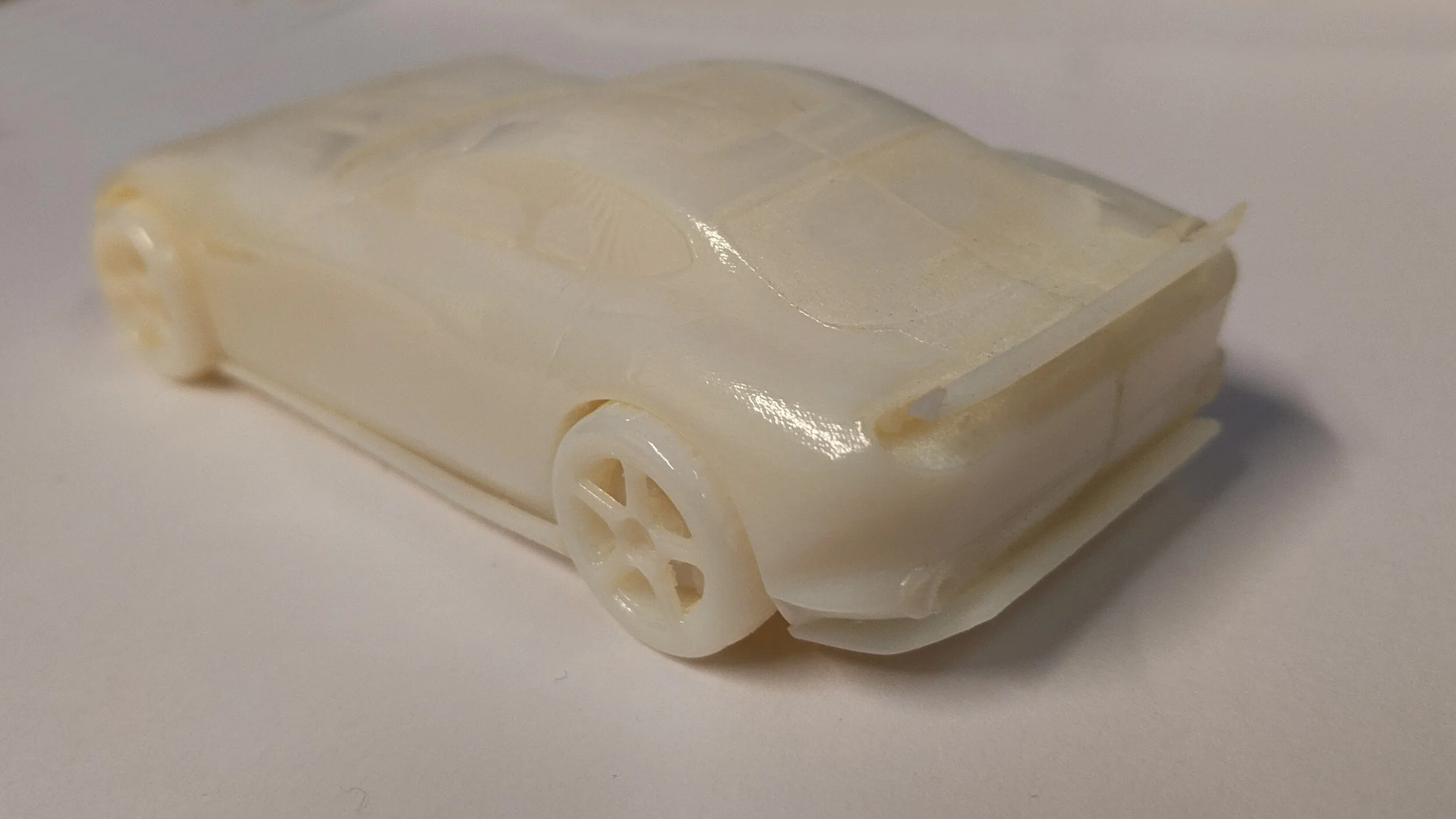
Parts are polyjet 3D printed for accurate detailing and parts are assembled with a little glue in the right places.